Laser marking on Foundries
Foundries are the basis of production for almost all industrial sectors.
They supply practically all types of factories that produce metal components, of all sizes and types. Let’s take a closer look at which sectors are involved and where laser marking can be found in this important industry.
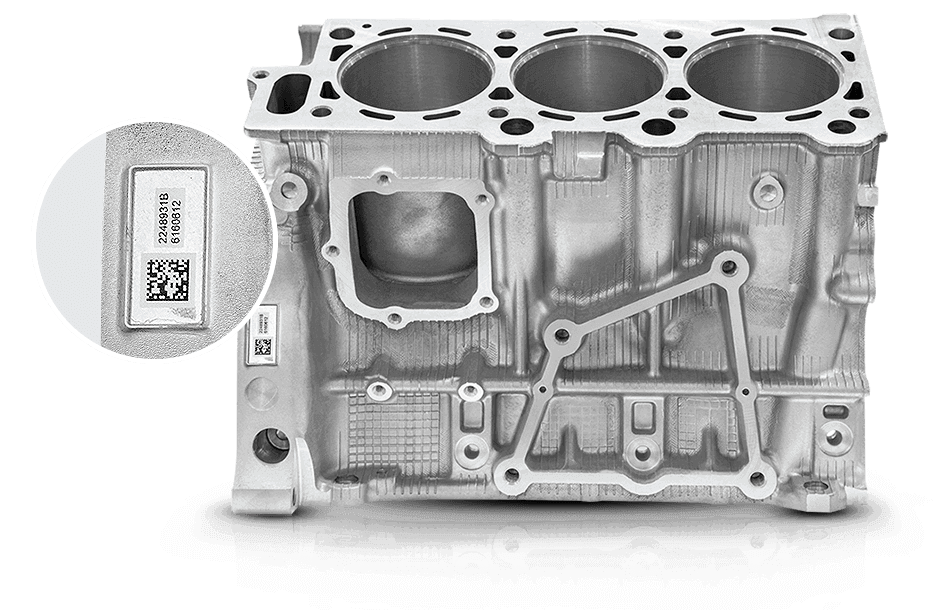
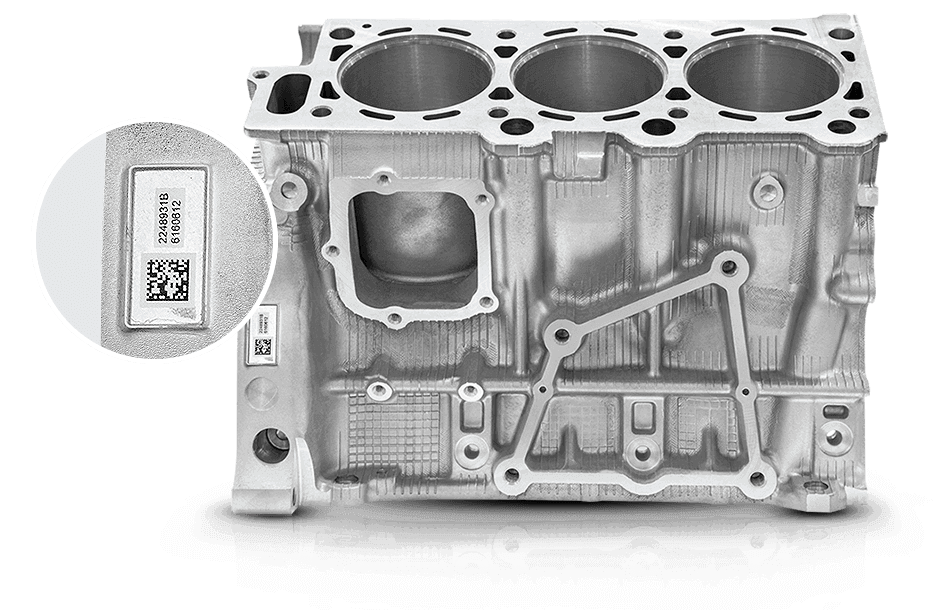
Automotive
The foundry is crucial in the automotive sector, producing structural components like engines, chassis, transmissions, and braking systems from ferrous alloys (cast iron and steel). Non-ferrous alloys, such as aluminum and magnesium, are also cast for structural parts and accessories like door handles made from zamak.
In the motorcycle sector, cast parts made from non-ferrous alloys like aluminum and cast iron are essential for engines and frames, with aluminum and zamak widely used for accessory components such as levers and headlights.
All vehicle components are marked with traceability codes, especially in the automotive sector. These two-dimensional DataMatrix codes contain vital information such as production lot, date, time, and factory of origin, ensuring quality and prompt service in case of faults.
Foundry Industry's Essential Role in Various Sectors
Modern airplanes and helicopters rely on cast steel, aluminum, and magnesium alloy components, produced using lost-wax precision casting technology, for powerful propulsion engines and other critical parts.
Electricity generation, from renewable sources like water and wind to fossil fuels, depends on cast steel and cast iron components. Turbine impellers and drive belts made from these materials transmit propulsion to power generators in hydroelectric, thermoelectric, and wind power plants.
The foundry industry provides essential components for urban safety and functionality. Manholes, street lamps, and park benches, all made of cast iron, ensure safe access to utilities, illuminate public spaces, and offer places to rest.
Stoves, boilers, bathtubs, and many household appliances like refrigerators, washing machines, and stovetops rely on cast components. The foundry industry indirectly supports domestic well-being and daily convenience.
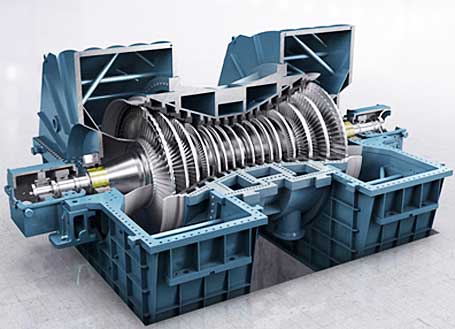

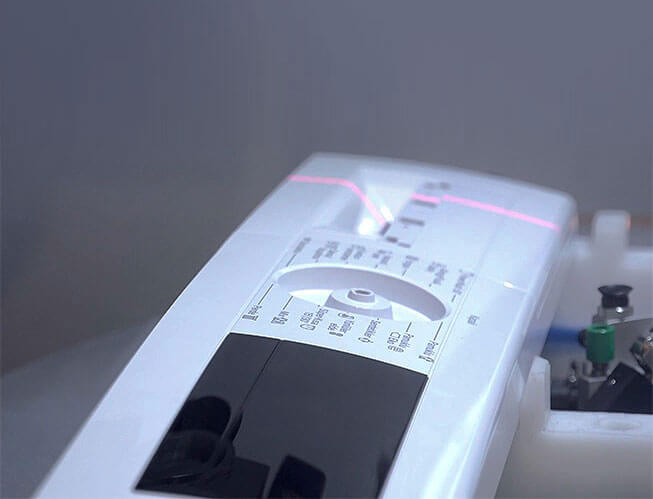
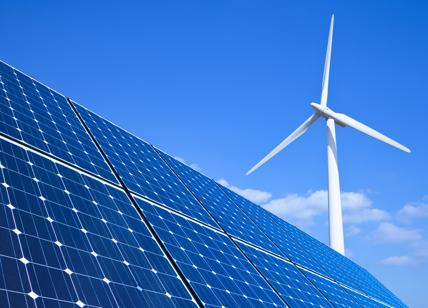
Ecology
The percentage of recycled materials used to replace the virgin raw material has steadily increased in recent years.
In Italy, particular attention has been paid to this topic and to the ecology of the system. Today, 75% of the materials used by the Italian foundry industry is recycled, for all those equipped with an electric furnace.
Production waste is also reused in the process: 95% of the soil used in the foundry is reused as raw material, replacing sand and soil from mining activities. Finally, 95% of the water used for furnace cooling is recovered and reused. A perfectly circular system, which makes foundries ecological businesses.
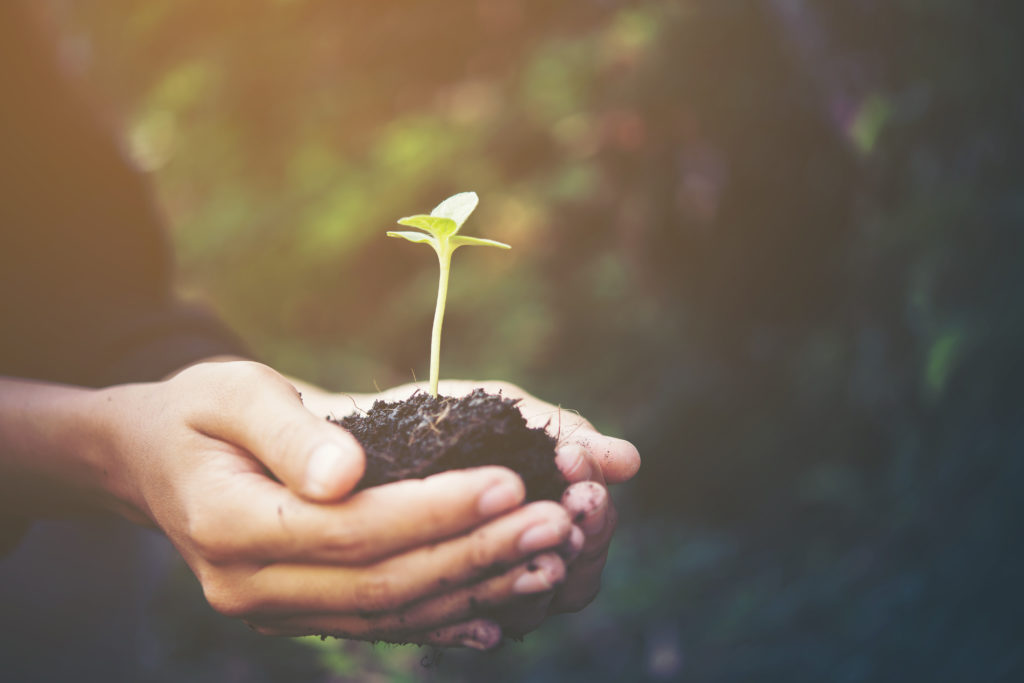
Laser marking on cast components
Laser marking now occurs in the casting process before sandblasting and shot peening. Until recently, this was impossible since these highly invasive processes damaged laser marking results and the code was illegible. The most popular traceability codes are DataMatrix. They are two-dimensional codes that have countless advantages over their one-dimensional equivalents, meaning barcodes.
First of all, DataMatrix codes can contain more than 2000 characters of information. For an equivalent yield, barcode dimensions would be too inconvenient for reading and its creation would be uneconomical.
Writing all this information in the DataMatrix means that a single code can trace: the production lot, the location, the date and time of dispatch, the information in the customer database. The type of datmatrix marked is an ECC 200 according to the AIM DPM standard. This is because laser marked codes are referred to as DPM that stands for Direct Part Marking. Laser marking takes place directly on the cast.
Another advantage of the DataMatrix is its error correction capability. It is readable even if 30% damaged. This characteristic on cast components takes on particular importance as we run this risk with the invasive shot peening and sandblasting processes.
The DataMatrix can be very small in size when made with the laser. Another important fact is that the DataMatrix is readable with a contrast of up to 20%. This is fundamental in the foundry world, where invasive processes such as sandblasting and shot peening could damage it.
At LASIT, we have developed a strategy to overcome this problem. Today, after years of Research and Development, we can mark the 2D code directly on the component that has just come out of the mold. This makes it traceable throughout its journey and the code remains legible even after sandblasting.
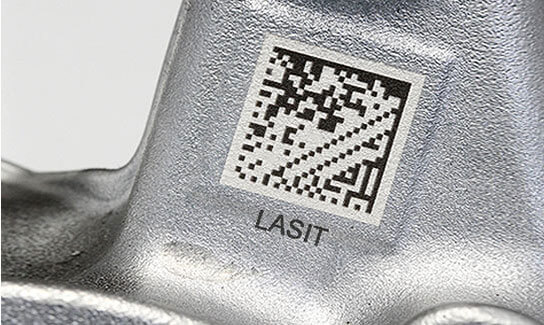
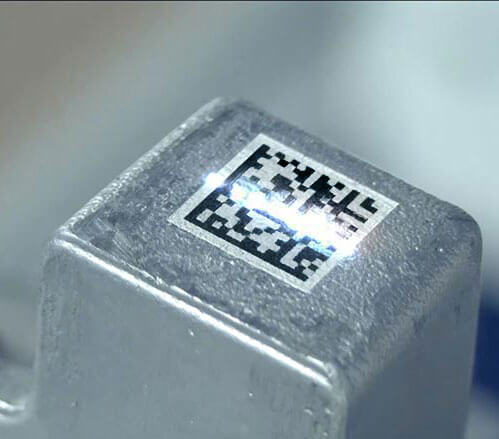
Our Advantages
Sole supplier | No intermediary, from design to realization |
Interface | PROFIBUS protocols, PROFINET and PROFIsafe |
Integration | Integrations with MES / ERP systems |
Industry 4.0 | Business database interaction for industry 4.0 |
Vision system | Automatic centering, 2D code verification and grading, OCR recognition |
Laser system | For every application and integration in production chains |